9 Hive WMS features to boost your 3PL company’s productivity
Are you seeking to boost the productivity of your 3PL company and cut your fulfillment costs? Simplify your fulfillment operations with Hive’s WMS.
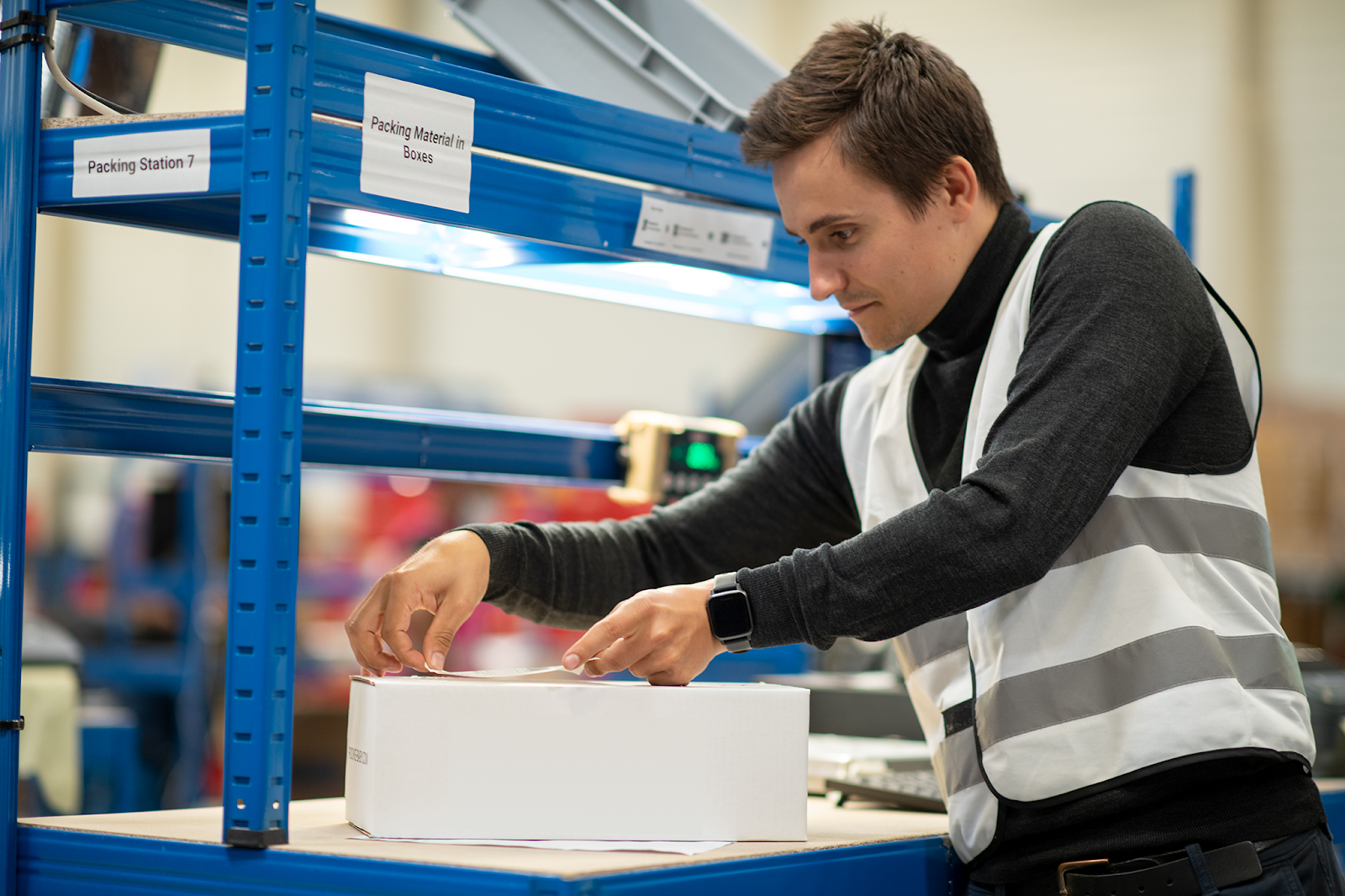
Hive WMS: Streamline your inventory management and fulfillment
Are you a 3PL company looking for a solution to fulfill orders efficiently, accurately and in a timely manner? Stand out from other 3PLs and streamline your fulfillment operations with a Warehouse Management System (WMS).
With a WMS you gain visibility into your day-to-day operations and manage your fulfillment workflow process; from inventory management to pick and pack, delivery, and more.
Hive’s WMS is specifically designed with e-commerce operations at its core. This means that it addresses the unique challenges and requirements of e-commerce fulfillment, such as:
- Efficient inventory management for not only SKUs but also flyers, stickers, and packaging materials. Ensure accurate tracking and availability of all components needed for order fulfillment.
- Effectively manage a wide range of SKUs and items, including large quantities for some of your customers and smaller numbers for others.
The WMS is continuously refined, tested and developed based on valuable feedback both from our e-commerce brands and associates working in our fulfillment center.
In this blog post we will explore 9 Hive WMS features to streamline and automate your 3PL operations:
1. Intuitive user experience focus to increase your day to day operations productivity
2. Pick and pack scan points to boost accuracy and efficiency
3. Group picking to boost your picking speed
4.Visual instructions for accurate order packing
5. Returns feature with an intuitive user flow
6. Batch tracking for better inventory management
7. Automated restocking to save you time and effort
8. Standardized kitting for order accuracy
9. Automated add-on rules for easier order fulfillment
9 Hive WMS features to boost your fulfillment efficiency
1. Intuitive user experience to increase your productivity
Reduce the time you spend onboarding new pickers and packers. Traditional onboarding methods require extensive training, involving hours of instructions before your workforce can effectively work in your fulfillment centers. This process can result in productivity delays.
Solve this issue and boost productivity with Hive’s WMS intuitive user experience. Onboarding your pickers and packers can be easily done in just 10 minutes thanks to an easy-to-use interface.
In Hive’s WMS associates see a confetti explosion on the screen every time upon completing a certain number of picks or packs. This fosters a sense of accomplishment, turning their work into a fun and rewarding activity.
Your new associates will perform their tasks efficiently without delays.
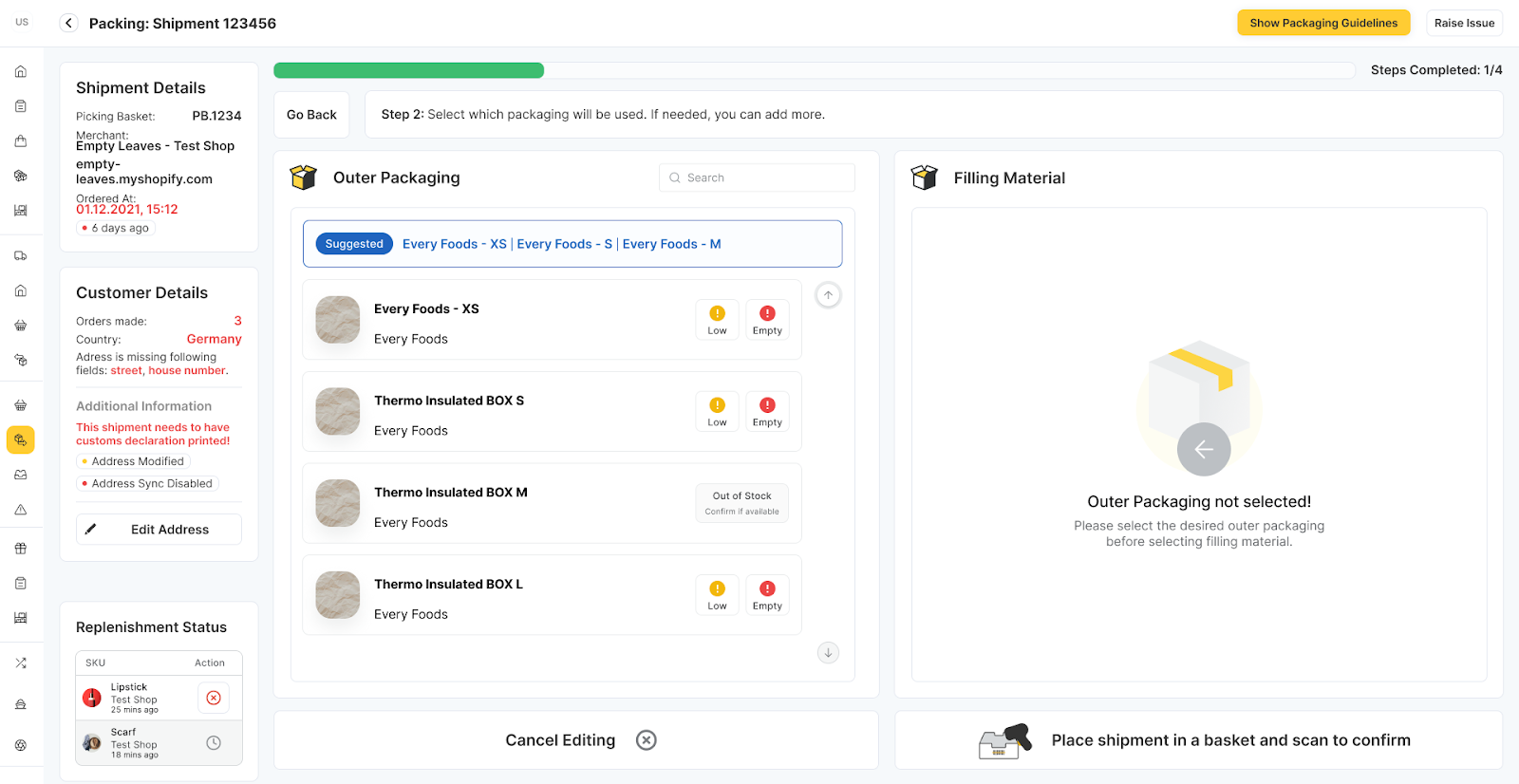
2. Pick and pack scan points to boost accuracy and efficiency
Manually tracking and managing your pick and pack can be challenging, especially when choosing whether to prioritize order accuracy or efficiency.
Find the right balance between accuracy and efficiency through SKU scan points.
With Hive’s WMS barcode scanners you can choose the approach that best suits you and your brands, whether you prefer to:
- Enforce scan points in both picking and packing processes to achieve the highest level of accuracy.
- Optimize for efficiency by skipping certain scan points.
- Increase flexibility by adjusting the item confirmation method on the SKU level, for example for items without barcodes.
By implementing scan points, manual tasks are reduced as barcode scanners automate SKU identification, saving time and ensuring precise tracking.
Experience fewer errors and improved order accuracy, eliminating the risk of manual data entry mistakes and enhancing customer satisfaction.
Stay updated on order progress and inventory levels with real-time pick and pack updates, enabling you to monitor stock movements and ensure efficient replenishment.
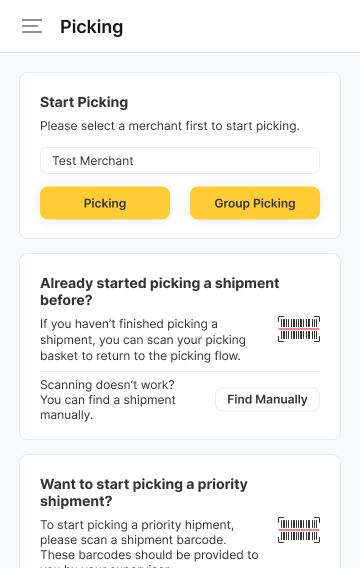
3. Group picking to boost your picking speed
Picking can be a time consuming process: save valuable time and increase your picking speed with group picking. Group picking is the process of grouping and picking similar shipments together. It reduces walking time and hence improves picking efficiency.
By using group picking, you achieve a 4x increase in speed compared to traditional picking methods.
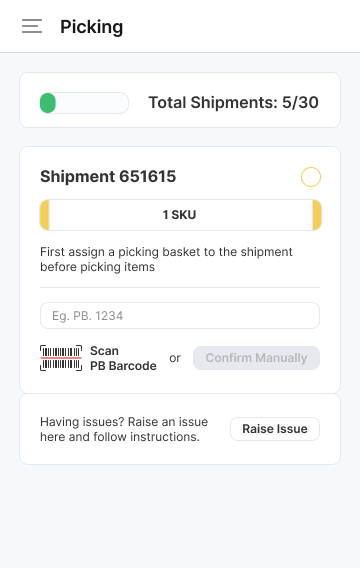
4.Visual instructions for accurate order packing
Maintain consistent quality across your packing operations through clear visual instructions.
Allow your customer to define instructions and provide pictures to your packers to minimize errors. By offering packing instructions, you can enhance packers’ understanding of their tasks. This improves packing accuracy and ensures a quicker fulfillment process.
The packing accuracy will increase your customers’ satisfaction and improve their end customer experience.
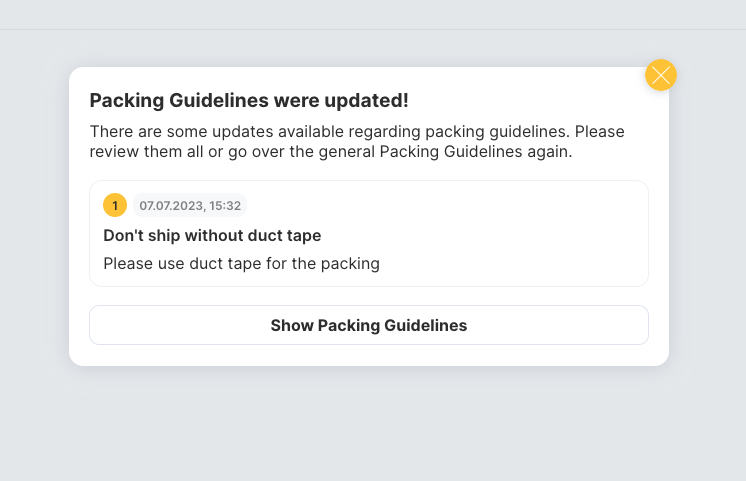
5. Returns feature with an intuitive user flow
Maintain control and transparency of returned items with an easy to use and intuitive return feature.
The return feature allows your customers to define follow-up actions based on item condition, ensuring that your workforce follows the correct steps and handles returns more efficiently.
By understanding the reasons behind product returns and evaluating their condition upon arrival at your fulfillment center, your customers will feel in control and have autonomy over their products.
You can also enable picture uploads of returned items. This will enable your consumers to visualize the products through the Hive app, making it convenient for them to assess the condition and make informed decisions regarding the next steps.
By speeding up the return process, Hive’s WMS reduces the operational costs associated with returns.
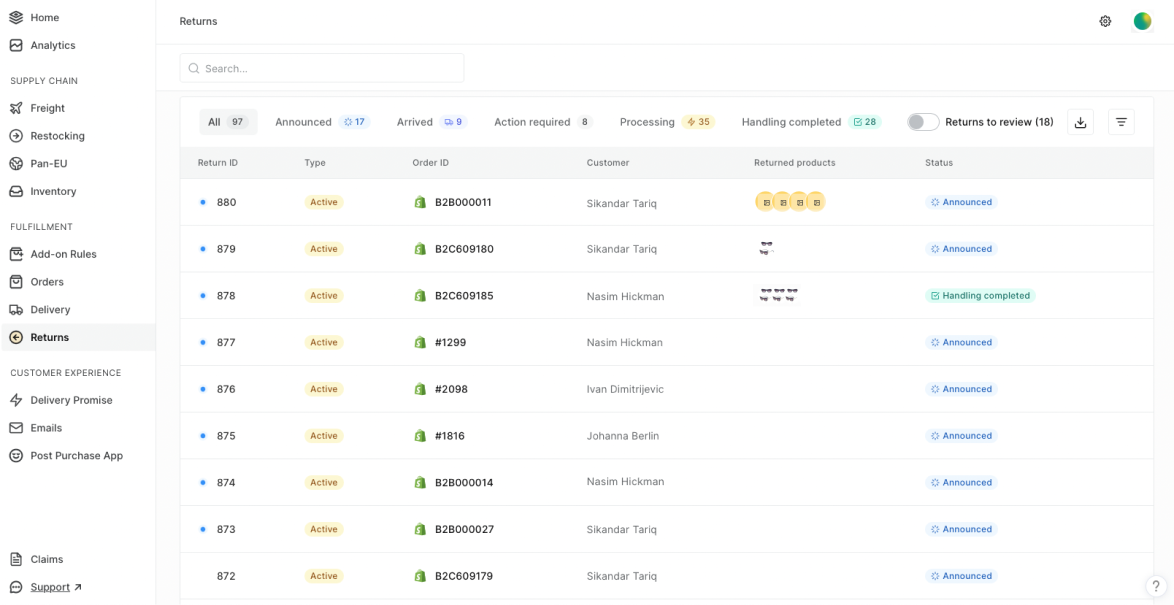
6. Batch tracking for a safer inventory management
Batch tracking allows your customers to efficiently monitor the origin of each SKU batch, mitigating the risk of unnecessary shipments due to concerns about product quality or expiration dates. This ensures timely deliveries and boosts end-customer satisfaction.
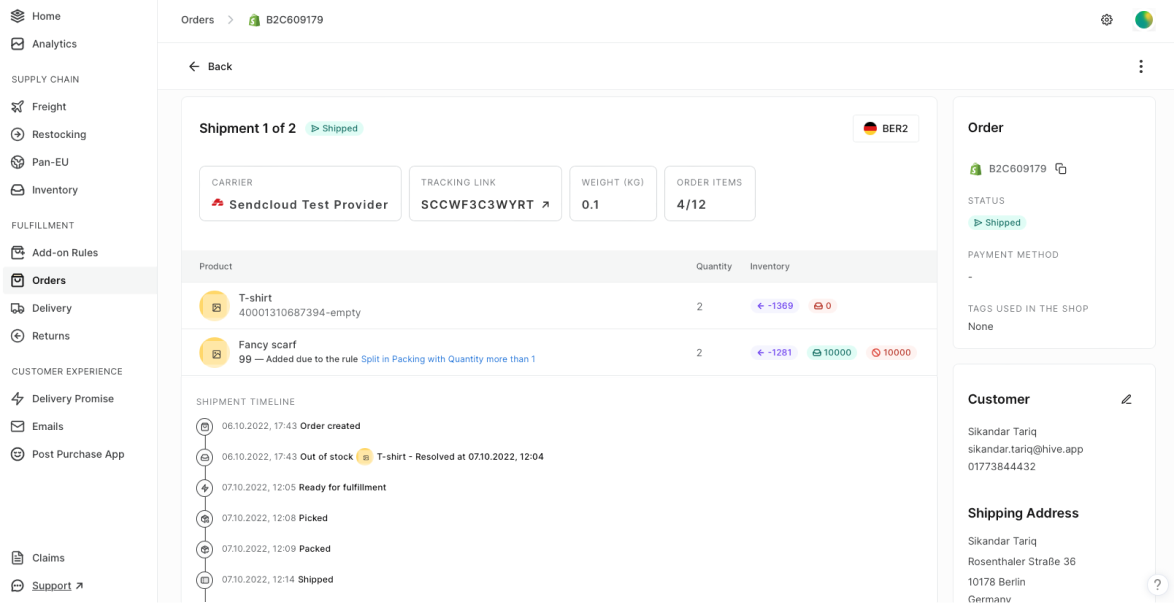
7. Automated restocking to save you time and effort
Manual restocking processes can be time-consuming and prone to errors. Solve this problem with automated restocking.
By allowing merchants to announce restocking shipments and providing a complete overview of the status update and item photos, automated restocking eliminates the need for time-consuming manual restocking processes.
Automated restock reminders operate through stages that align with your merchant’s stock status, allowing them to take swift actions based on the provided information about their stock level.
By simplifying the restocking process, automated restocking reduces errors and increases overall operational efficiency.
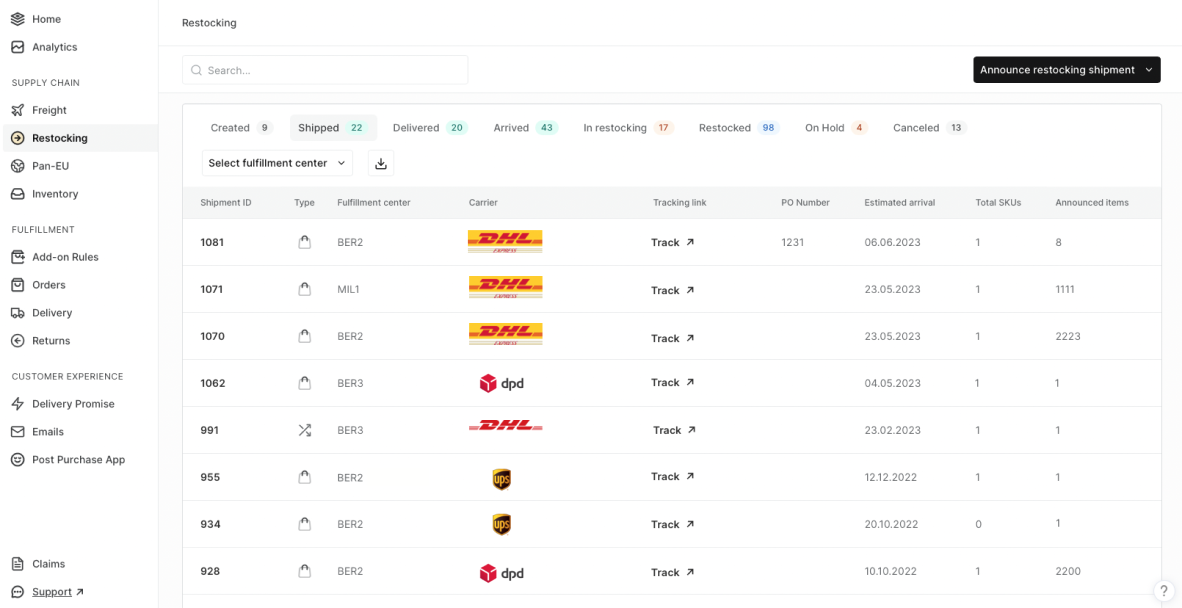
8. Standardized kitting for order accuracy
Kitting is an order fulfillment technique where instead of picking and packing individual items as orders come in, two or more items are pre-assembled into ready-to-ship kits.
Kitting reduces your fulfillment costs by turning a multiple pick process into a single pick process. However, managing kits can be challenging, especially when dealing with a diverse range of products and packages.
Hive's WMS kitting feature provides step-by-step guides and customer-provided photos. This efficient system enhances kitting accuracy.
With kitting you can review tasks before approval and request clarification from your customers on any ambiguous points. Getting these crystal-clear instructions will make sure processes run smoothly, and fosters a sense of trust between you and your customers.
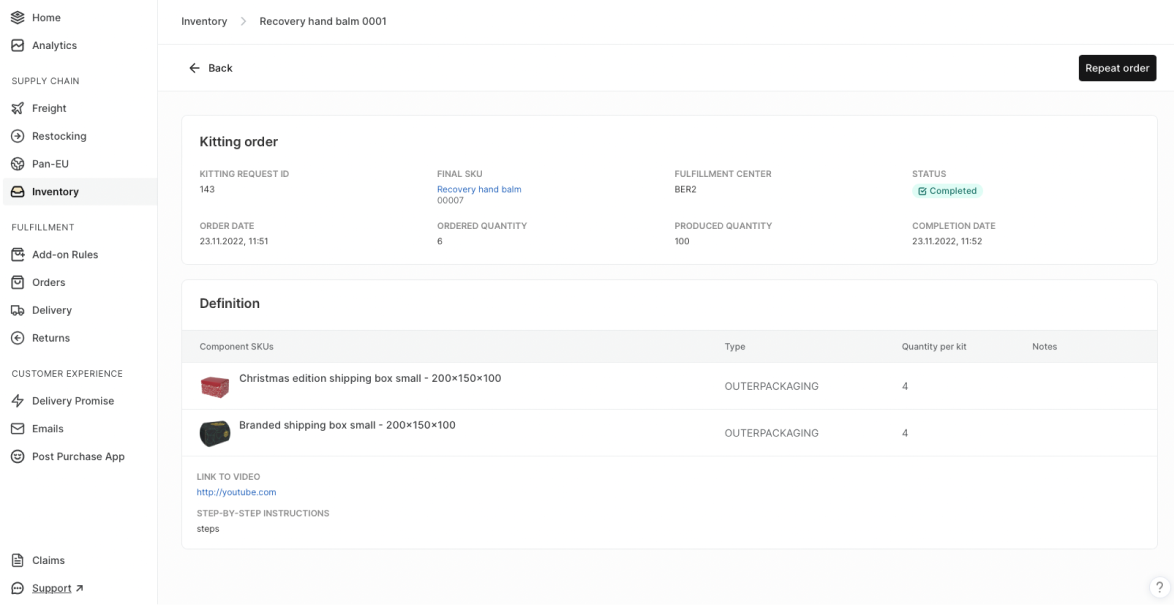
9. Automated add-on rules for personalized order fulfillment
Simplify the order fulfillment process for your associates with add-on rules.
Add-on rules are a set of automations which allow you to add certain extras to your orders based on variables such as order destination, time of order, or a specific SKU. You can find more details on add-on rules in this blog post.
By eliminating complicated setups, unnecessary communication, and packing errors, using add-on rules saves time and reduces wasted resources.
With add-on rules, your customers have the flexibility to define their own rules, eliminating the need for manual communication and ensuring that any changes are automatically incorporated into the pick and pack process.
You can fine-tune the insertion strategy (either during picking or packing) to strike the perfect balance between accuracy for complex rules (e.g. value-based orders) and efficiency for standard rules (e.g. applying to every order).
Automatically handle out-of-stock add-on items according to your customers preferences. Your customers choose to either block fulfillment or ignore add-on items when they are out of stock, streamlining the process.
The implementation of new add-on rules and any changes takes effect with a one-day delay, giving you ample time to prepare your packing stations accordingly.
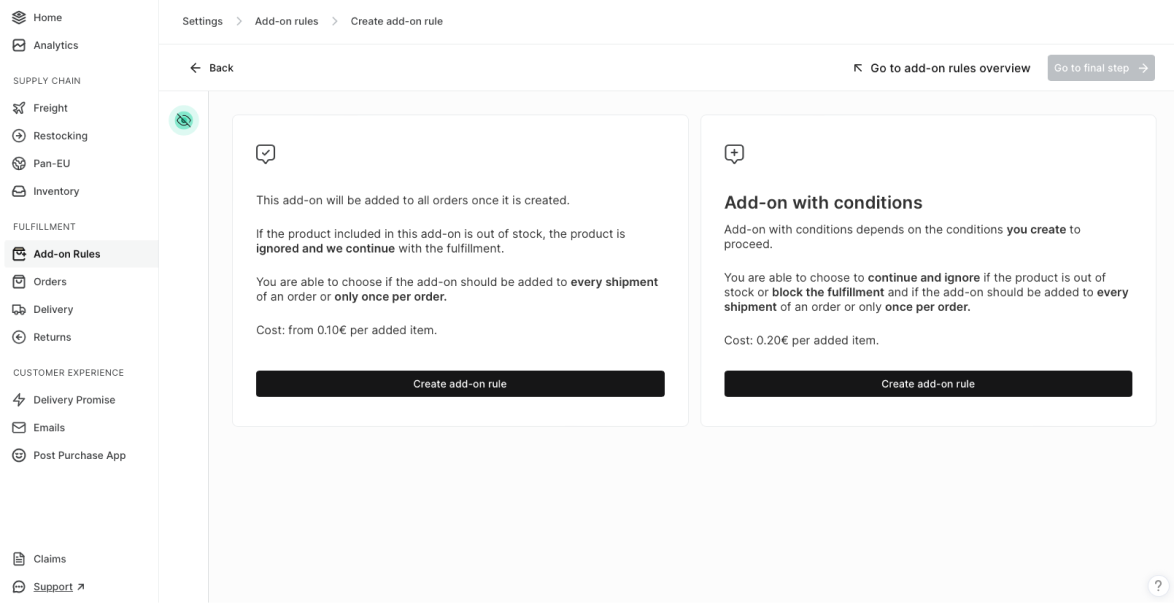
Boost your productivity by efficiently managing your inventory with Hive’s WMS
Improve your fulfillment with Hive’s scalable and flexible WMS. By leveraging Hive's tailored fulfillment solutions, you can increase your inventory accuracy and overall processes efficiency. From optimizing picking speed to an intuitive user experience for your onboardings, Hive empowers your 3PL to streamline your inventory management.
Discover more about Hive’s fulfillment processes here or request a quote to see how Hive can benefit your 3PL today.