11 features of the Hive WMS that help you scale your e-commerce brand
Are you seeking to improve your inventory management and increase your overall customer satisfaction? Experience better fulfillment and overall control of your inventory with Hive’s WMS.
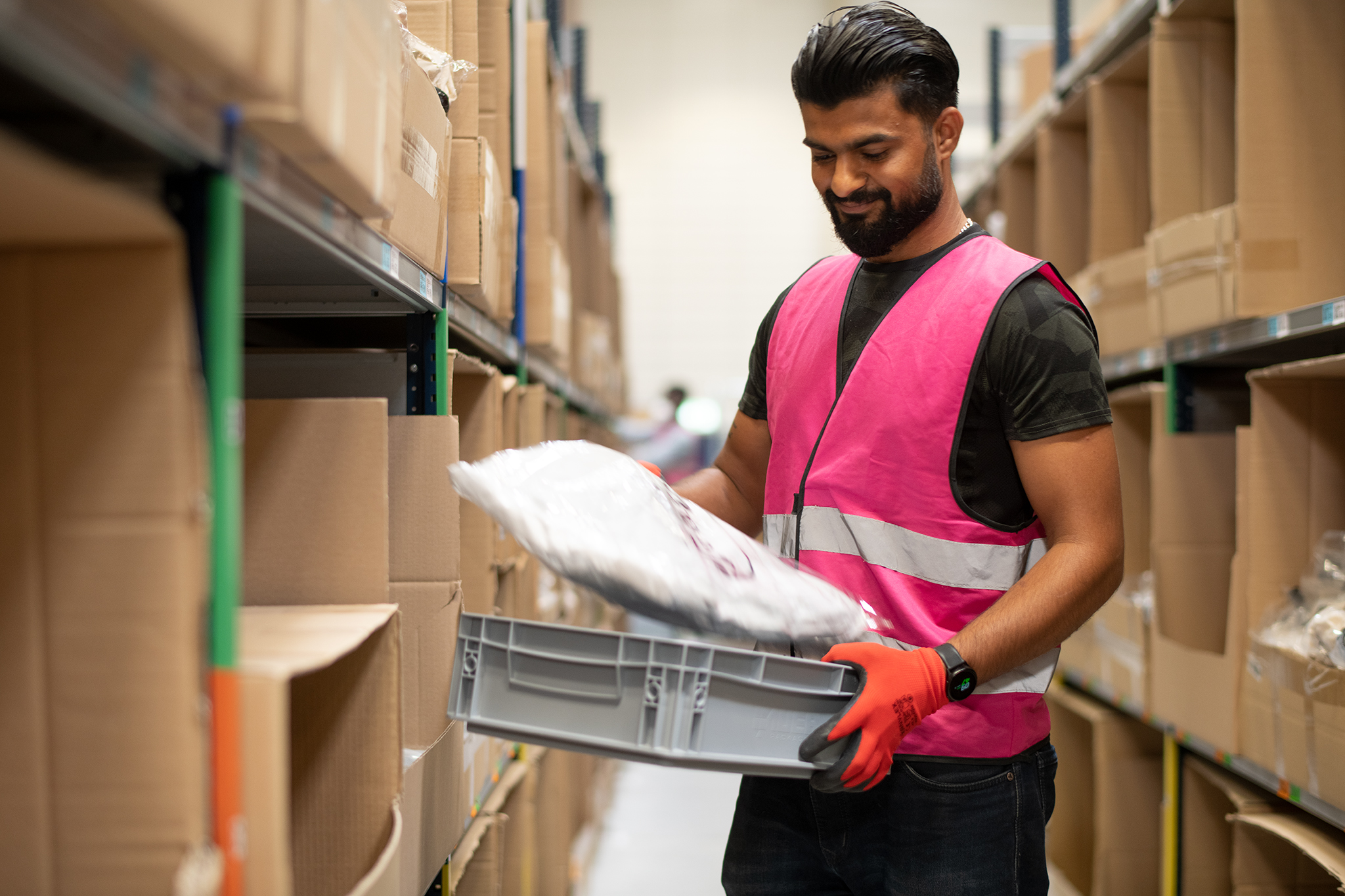
Hive WMS: Flexible and scalable to help you grow your brand
Are you tired of the chaos and frustration that comes with managing your inventory with a 3PL partner who relies on a subpar WMS? Do you find yourself drowning in lost orders and overselling because of intransparent inventory management?
Imagine a world where you can effortlessly track your products, streamline your logistics operations, and have complete control over your inventory. This could be your reality with Hive’s warehouse management system (WMS).
With a WMS, you gain real-time visibility and control over your inventory, enabling efficient management of stock levels, order fulfillment, and warehouse resources.
Hive’s WMS is specifically designed with e-commerce operations at its core. This means that it addresses the unique challenges and requirements of e-commerce fulfillment, such as:
- Efficient inventory management for not only SKUs but also flyers, stickers, and packaging materials, ensuring accurate tracking and availability of all components needed for order fulfillment.
- The ability to handle campaigns and support peak times digitally, allowing for management of increased order volumes and promotional activities without compromising fulfillment efficiency.
The WMS is continuously refined, tested and developed based on valuable feedback both from our ecommerce brands and associates working in our fulfillment center.
In this blog post we will explore 11 Hive WMS features to scale your brand:
- Group picking for faster fulfillment
- Balance your accuracy rate and efficiency through pick and pack
- Increase your customer satisfaction with seamless kitting
- Improve your packaging with easy and flexible add-ons
- Ensure product quality by uploading visual instructions for the packers
- Gain full control and transparency of your products with our returns
- Enhance customer satisfaction through partial fulfillment
- Automated restock reminders
- Manage your inventory safety with batch tracking
- User experience focus for efficient picker/packers onboarding
- Gamification of Pick and Pack
11 Hive WMS features to scale your brand
1. Group picking for faster fulfillment
Picking often consumes a significant amount of time due to repetitive walking to distant picking locations. Group picking is the process of grouping and picking similar shipments together. It reduces walking time and hence improves picking efficiency.
For example, Imagine your picker has to pick 30 times the same SKU for 30 different orders. Instead of doing the same repetitive walking and picking process 30 times, they can pick the same SKU 30 times in a row without walking to any different picking location.
This can lead to a 4x increase in speed compared to the traditional picking flow.
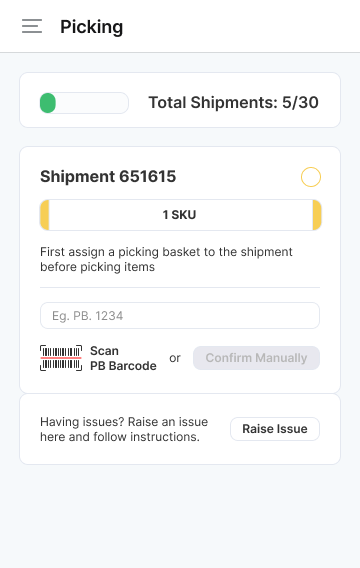
2. Pick and pack scan points to boost your accuracy rate and efficiency
Finding the right balance between pick and pack accuracy and efficiency can be challenging. An easy way to achieve this is through SKU identification methods, such as scan points.
With Hive’s WMS you have the freedom to choose the approach that best suits your brand’s requirements, whether you prefer to:
- Enforce scan points in both picking and packing processes to achieve the highest level of accuracy.
- Optimize for efficiency by skipping certain scan points.
- Increase flexibility by adjusting the item confirmation method on the SKU level, which is particularly useful for items without barcodes.
Implementing scan points means you avoid unnecessary errors, and reduce mispicks.
By reducing these errors, you increase your fulfillment speed and minimize the time spent on correcting mistakes. This improvement in pick and pack accuracy contributes to a higher customer satisfaction rate by providing customers with correct packages in a timely manner.
Improved accuracy also allows for a decrease in returns and redeliveries, resulting in a more efficient and cost-effective fulfillment process.
With Hive’s WMS scan points, you can enhance accuracy and tailor the picking process to your brand’s priorities.
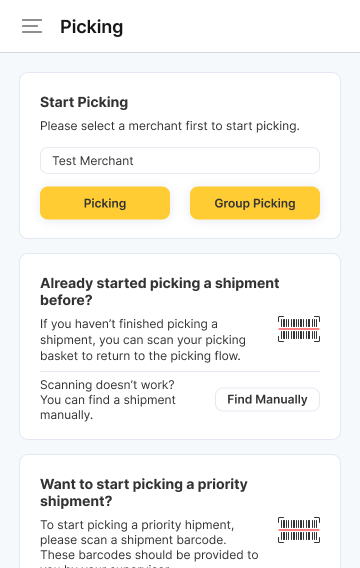
3. Kitting to increase customer satisfaction
Kitting is an order fulfillment technique where, instead of picking and packing individual items as orders come in, two or more items are pre-assembled into ready-to-ship kits.
Kitting can reduce your fulfillment costs by turning a multiple pick process into a single pick process. However, managing kits can be challenging, especially when dealing with a diverse range of products and packages.
You can eliminate these struggles and fulfill orders swiftly through Hive’s seamless kitting flow.
Improve your kitting process and:
- Gain the flexibility to personalize your kitting requirements according to your preferences.
- Increase your inventory accuracy by tracking and managing kitted products more efficiently.
- Upload visual instructions, such as pictures and videos of kitting through our WMS, which allows associates to have a clear understanding of the kitting assembly process.
- Adapt and incorporate changes and feedback quickly, ensuring your flexibility.
By leveraging Hive's kitting, you can enhance customer satisfaction through a high order accuracy rate. Furthermore, you can optimize your fulfillment speed and reduce costs by efficiently implementing changes.
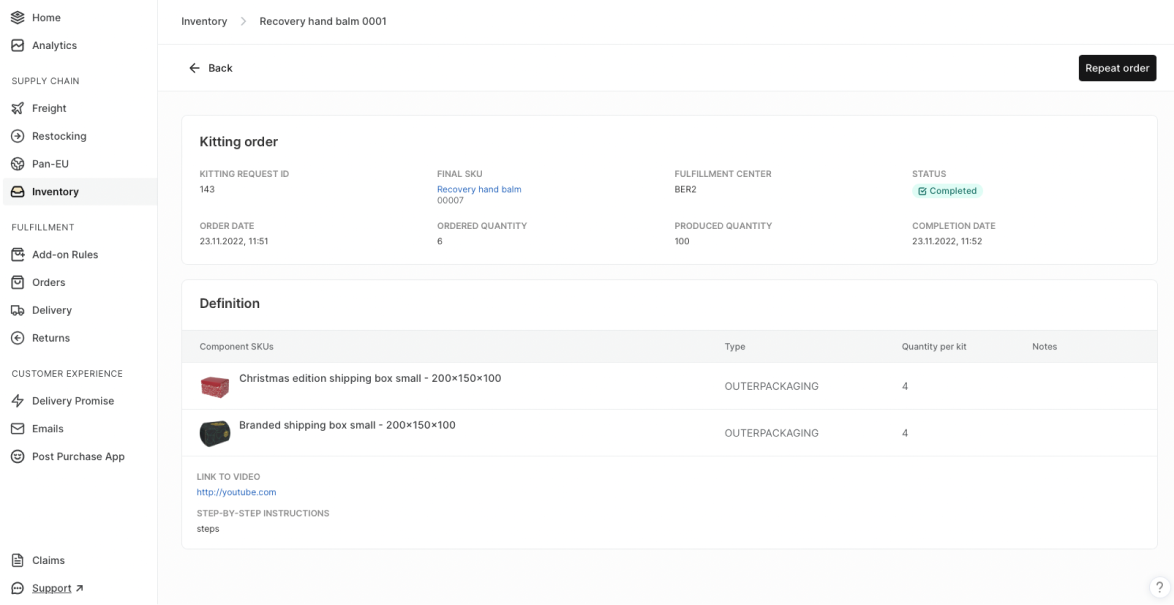
4. Leverage your packaging with easy and flexible add-ons
Increase your customer lifetime value (LTV) by customizing your packaging with add-on rules. Add-on rules are a set of automations which allow you to add certain extras to your orders based on variables such as order destination, time of order, or a specific SKU. Find more details on add-on rules in this blog post.
Add-on rules let you personalize the customer journey in just a few clicks, resulting in a more engaging and impactful experience. Save time by utilizing add-on rules instead of engaging in multiple conversations and waiting for implementation with your 3PL partner. Eliminate the need for back-and-forth communication and delays.
Add-on rules bring you both monetary benefits and foster your customer loyalty.
For example, with add-on rules you can reward your customers with a free gift on orders above a certain basket value, which encourages your customers to spend more. Nearly 90% of free gift receivers said they were “somewhat likely” to buy more frequently from an online retailer after receiving a gift.
Incorporating free gifts, flyers, and promotions of new products into your packaging helps build a strong community by creating a sense of goodwill and excitement among customers, fostering brand loyalty, and encouraging word-of-mouth recommendations and engagement with your brand.
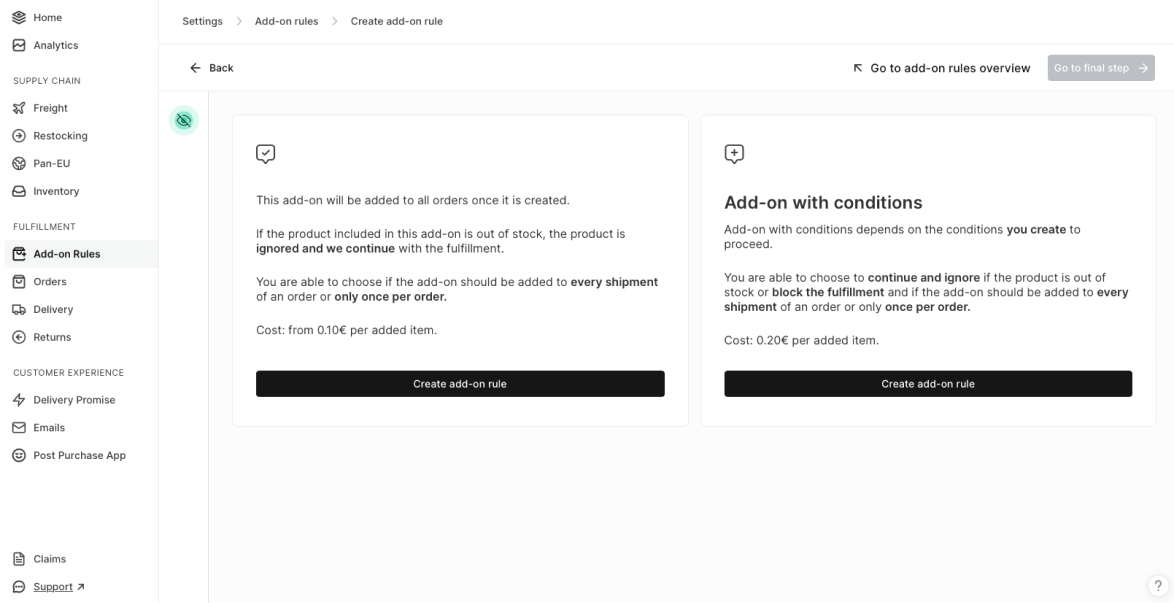
5. Quality assurance through visual instructions for the packers
Make sure your customer receives quality products by providing instructional videos and pictures to your packers.
By providing video instructions and pictures, you can increase your customer satisfaction through a consistent brand experience with your packaging. This will foster trust and loyalty among your clientele.
Moreover, by providing visual instruction, you will help your packers onboard easily to your packaging standards and processes. This reduces the learning curve and expedites their productivity, leading to improved efficiency and faster order fulfillment.
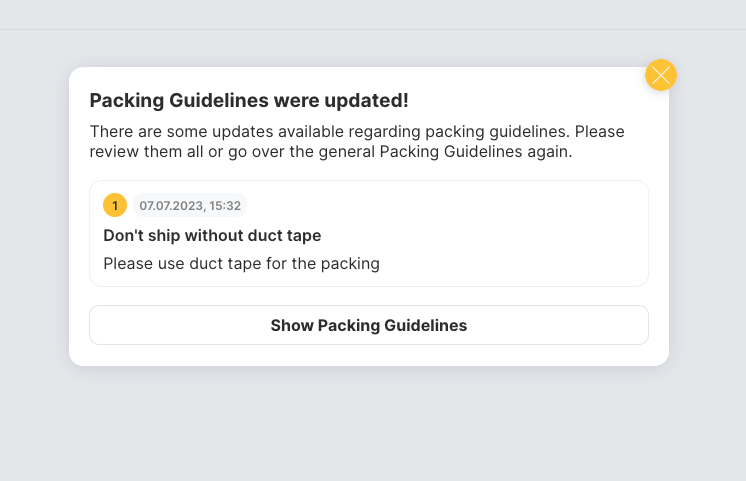
6. A returns feature gives you full control and transparency
It is inevitable that your products might get returned, so having an effective returns strategy in place is key.
Understanding the reasons behind product returns and evaluating their condition upon arrival at your fulfillment center is crucial for resolving potential issues.
To achieve control and transparency over your products, Hive’s return feature allows you to establish follow-up actions based on product conditions, guiding your workforce through the necessary steps.
Get pictures uploaded by fulfillment center staff to the WMS of all returned items and visualize them through the Hive app. This way, you can easily assess the state of your products and decide what to do next. Or, you can save valuable customer support time by implementing automatic return guidelines.
Reduce your return rates by constantly evaluating and checking the condition of your returned products, and elevate your customer experience by giving your customers high quality products.
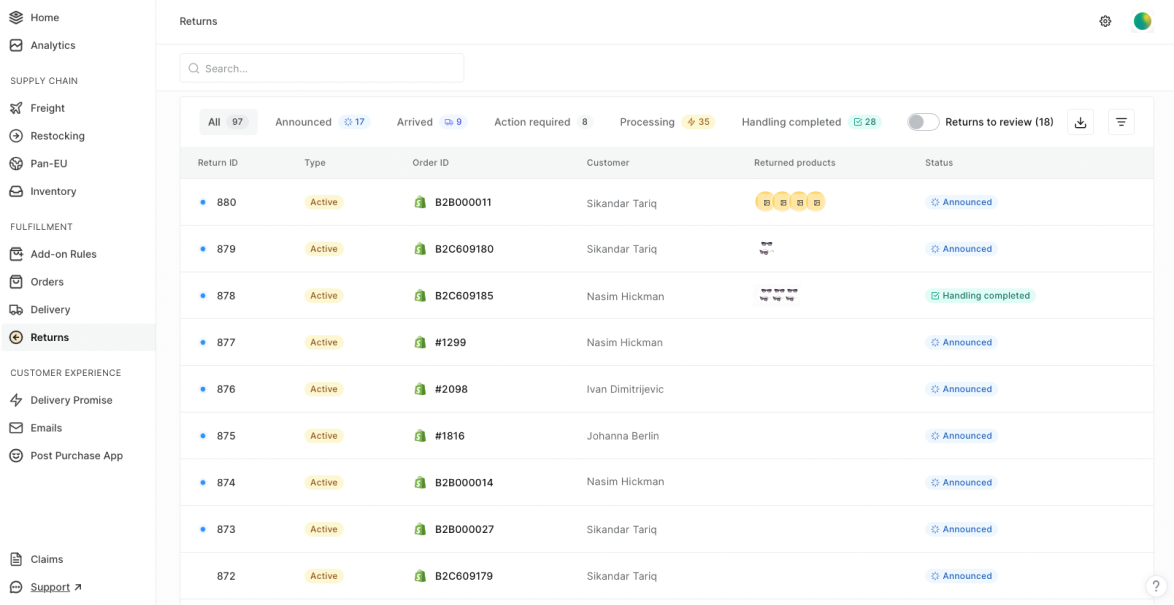
7. Partial fulfillment for higher customer satisfaction
When a specific SKU is unavailable, it is crucial to avoid disappointing customers who eagerly await their orders. Implementing partial fulfillment ensures you never let them down.
Partial fulfillment means separating your customer’s order so that they can receive in-stock SKUs on time, and not have to wait for the out-of-stock SKU to become available.
This approach not only safeguards your brand reputation but also fosters customer loyalty by demonstrating your commitment to meeting their needs.
Employing partial fulfillment also helps you retain valuable customers who appreciate your proactive efforts to fulfill their orders, even in the face of inventory shortages.
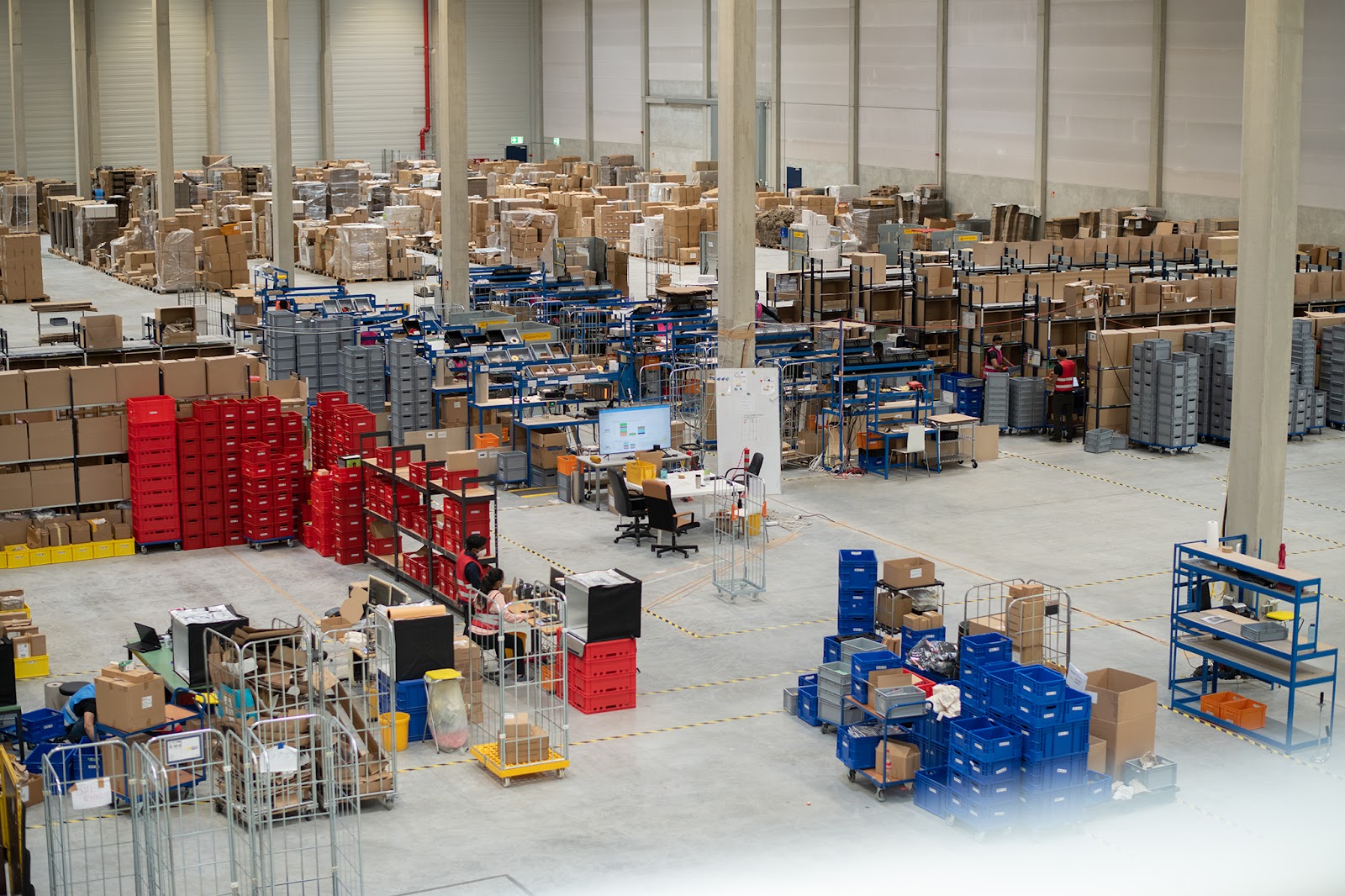
8. Automated restock reminders
Inadequate restocking processes can lead to stockouts, which in turn result in lost sales, reduced profits, and a tarnished brand reputation.
With automated restocking reminders, you can easily manage your inventory and ensure that you never run out of stock.
Automated restock reminders operate through distinct stages that align with your stock status, allowing for swift actions based on the provided information. By leveraging it, you can access detailed information about your stock levels and receive timely notifications when a SKU is running low.
Efficiently manage inventory and make informed restocking decisions with automated reminders, streamlining the process and saving valuable time and resources..
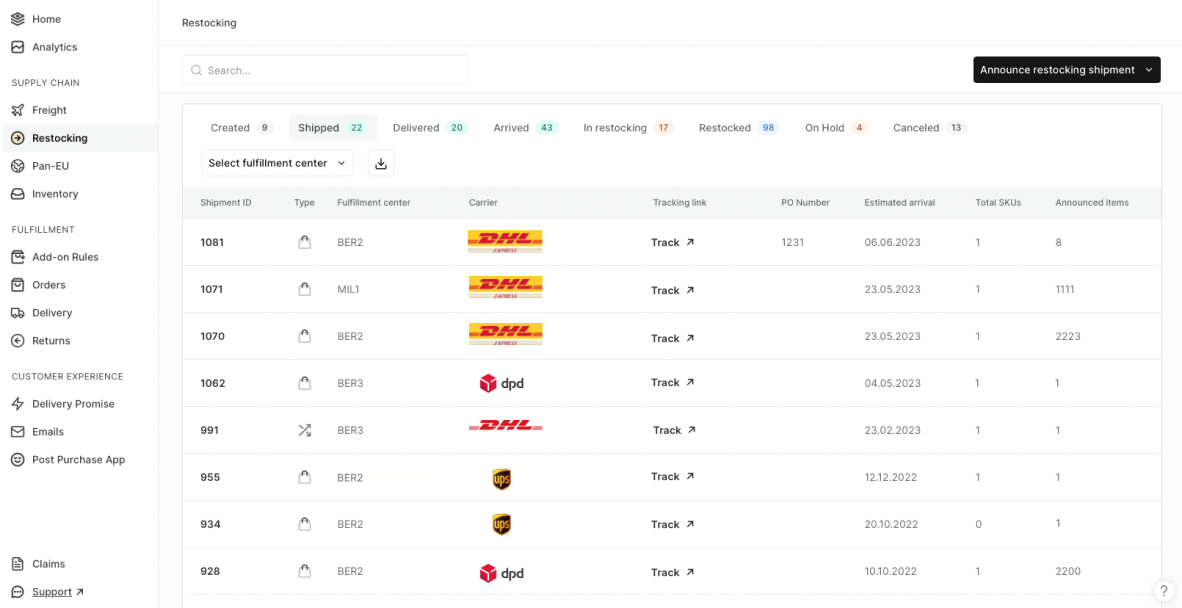
9. Batch tracking to manage your inventory safety
Managing inventory and tracking expiration dates can be burdensome, particularly when handling perishable items like food and personal care products.
Luckily, batch tracking provides a solution to this challenge.
With batch tracking, you can efficiently monitor the origin of each SKU batch, mitigating the risk of unnecessary shipments due to concerns about product quality or expiration dates. This proactive approach ensures effective resolution and minimizes disruptions, safeguarding your business operations.
Batch tracking not only ensures timely delivery but also boosts customer satisfaction through consistent and reliable product shipments by providing real-time visibility and control over the movement of multiple items within a batch.
Additionally, efficient inventory management through batch tracking provides a competitive advantage when planning new orders and marketing campaigns by offering valuable insights into inventory availability and movement. It allows brands to analyze inventory levels, and make informed decisions when planning new orders and designing marketing campaigns.
By having accurate and up-to-date information on your inventory, you can make informed decisions and optimize your resources, maximizing profitability and minimizing waste.
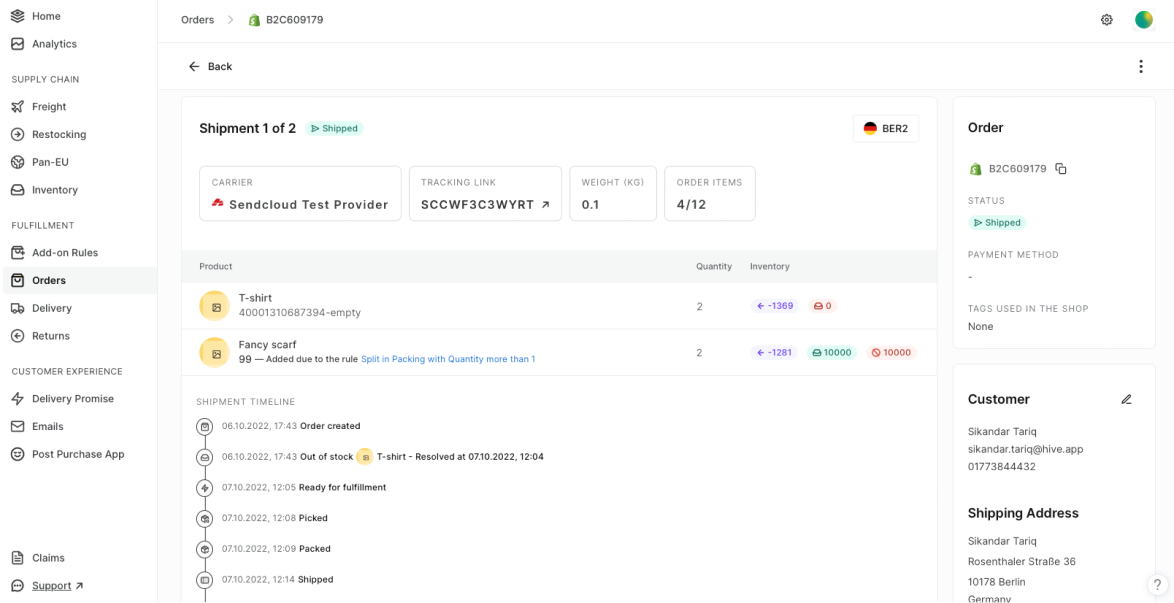
10. User experience focus for efficient packer onboarding
Onboarding new packers is complex and time consuming. Traditional onboarding methods require extensive training, involving hours or even days of instruction before new employees can effectively perform their duties. This process can result in productivity delays and increased cost for businesses.
That is why Hive’s WMS focusses on user experience. The onboarding of your packers can be done within minutes. Packers can see visual and video instructions with your specific packing guidelines through the WMS. Its straightforward navigation enables packers to quickly understand and familiarize themselves with the system.
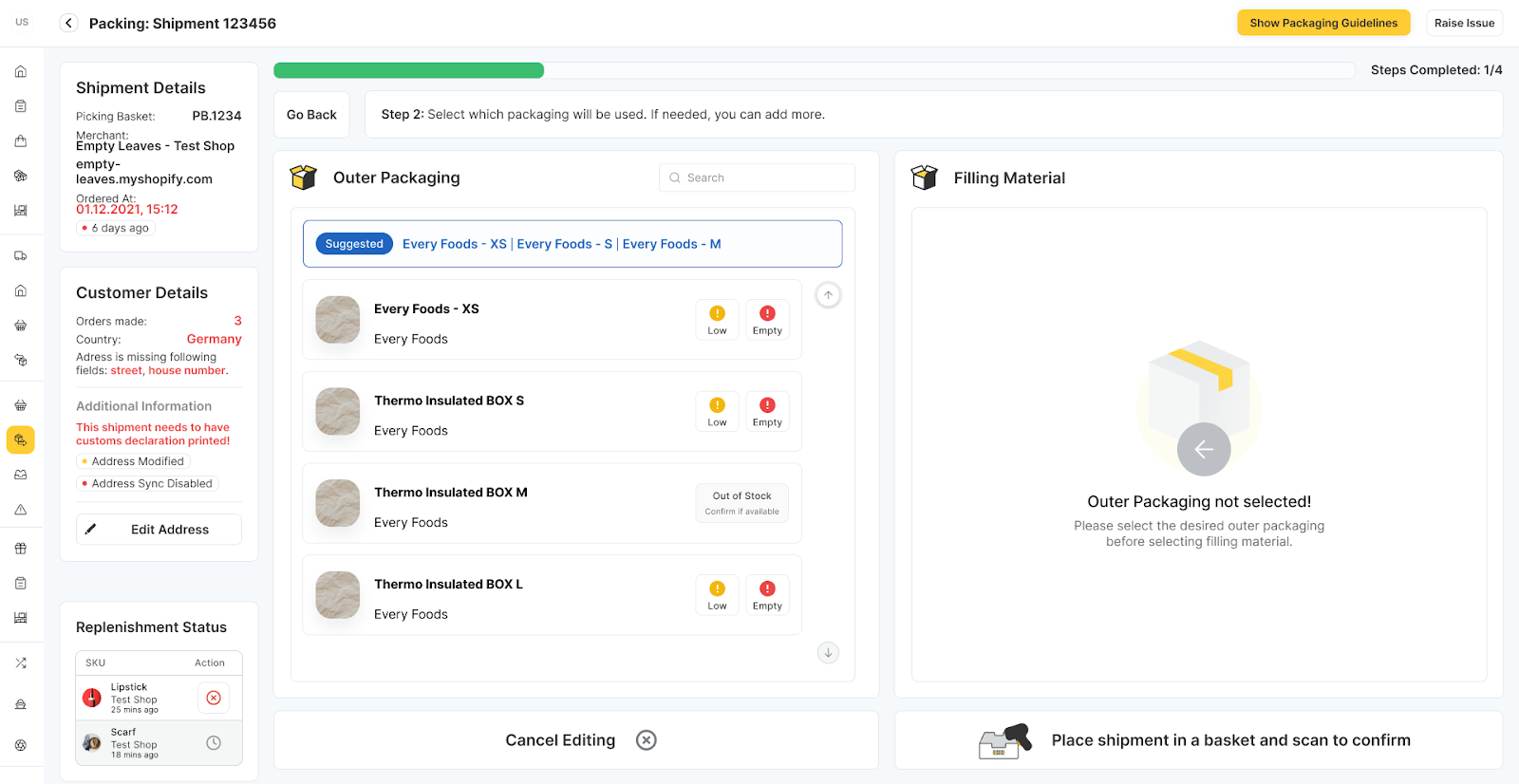
11. Gamification of pick and pack - for more fun and efficiency
By implementing gamification, or a reward system, into the pick and pack experience, the job becomes more fun with tiny rewards when finishing a task.
In Hive’s WMS pick and pack feature, associates see a confetti explosion on the screen every time they complete a certain number of picks or packs. This gamified approach provides a sense of accomplishment, transforming the work into a fun and rewarding activity.
Associates appreciate the acknowledgment and feel motivated to achieve more.
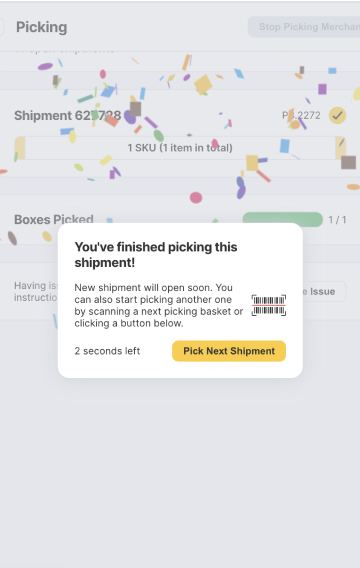
Save time and money by efficiently managing your inventory with Hive’s WMS
Scale your brand with Hive’s flexible WMS. By leveraging Hive's tailored fulfillment solutions, you can optimize your processes and elevate your brand's growth trajectory. From streamlined inventory management to seamless picking and packing of orders, Hive empowers your brand to efficiently fulfill customer demands.
Discover more about Hive’s fulfillment processes here or request a quote to see how hive can benefit your brand today