Picking at Hive: the ultimate guide to how picking is managed to optimize your fulfillment
An insider view into how picking is managed and strategized at Hive to optimize fulfillment for e-commerce brands
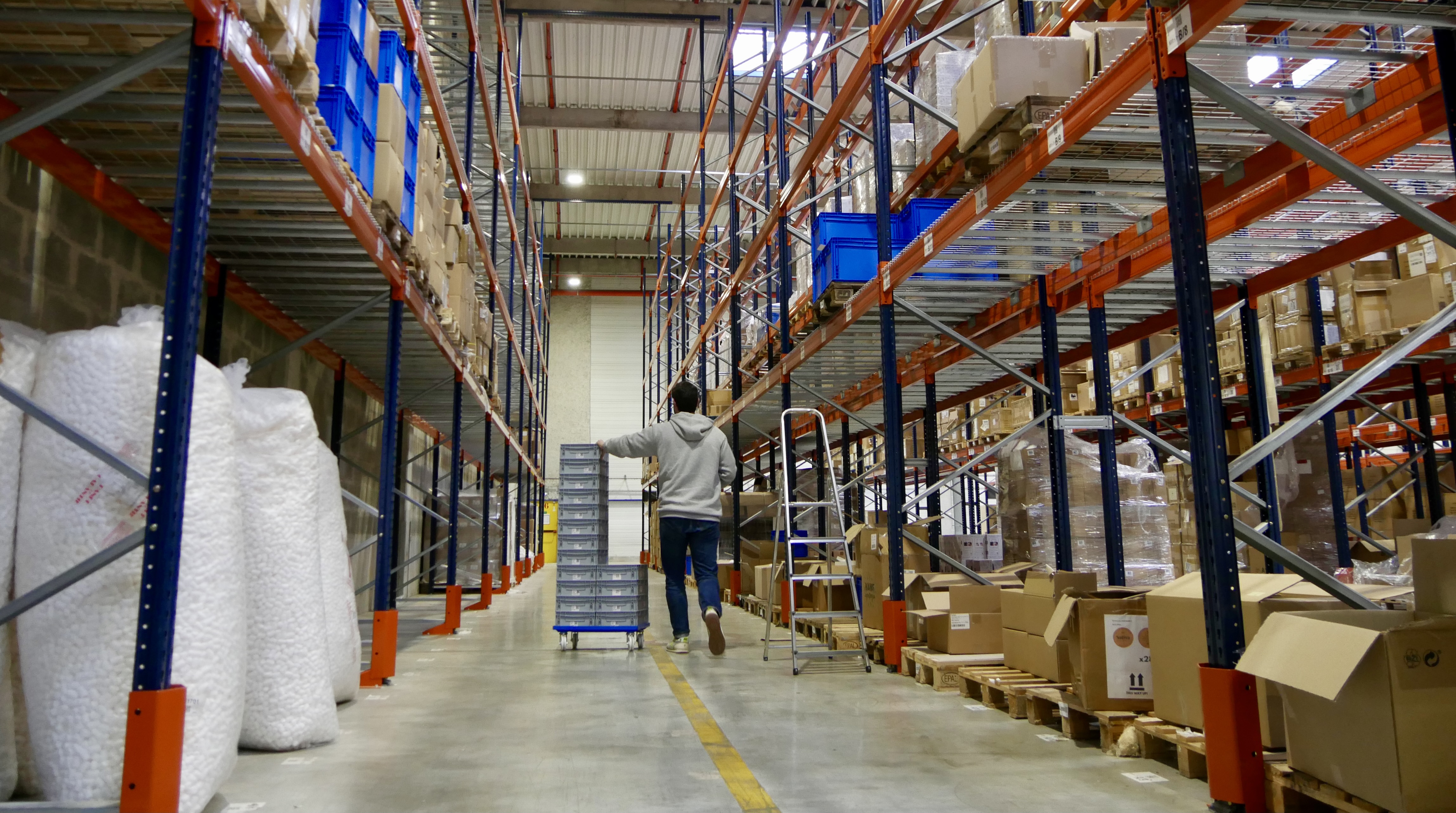
Picking in e-commerce logistics
Picking, refers to the systematic process of selecting items from a warehouse inventory to fulfill customer orders. When customers create an order, the fulfillment process is initiated with picking, where SKUs in the order are chosen from shelves and pallets, ready to be packed and shipped.
However, picking goes beyond the selection of products; it extends to optimizing the entire fulfillment process. Understanding and enhancing the picking process is a crucial step for companies looking to stay competitive in the dynamic e-commerce world.
In this article, you will get a deep dive into the intricacies of picking in fulfillment and how Hive’s warehouse management system (WMS) is in constant evolution to optimize your fulfillment.
This article will be covering the following topics:
- Why is picking so important in fulfillment?
- How your brand benefits from the broad set of picking strategies within the Hive WMS
- Why picking at Hive is the best solution for your brand
Why is picking so important in fulfillment?
An optimized picking strategy can be the differentiating factor between a returning customer and one that refuses to buy from your brand again. It impacts your order accuracy and fulfillment speed.
Optimizing picking methods is a way to reduce human-error and ensure that customer orders arrive on time, and with the correct products. This in turn creates a positive customer experience and can have a strong impact on your brand’s reputation.
After all, a happy customer is one that buys again, that will talk about your brand, leave positive reviews and even post about it on social media.
Having accurate orders will also positively impact your returns rate, meaning you and your customer support team will spend less time dealing with incorrect packages, refunds, and exchanges.
How your brand benefits from the broad set of picking strategies within the Hive WMS
Single Shipment picking
The single shipment picking method is the standard picking solution where the picker works by picking the different SKUs per shipment. This method is based on a FIFO setup (First-In-First-Out), so the first orders are the first to be picked to be shipped off.
This picking method works per shipment where one picking basket is attributed to each shipment. Just like in the following picking methods discussed below, each order has its own picking basket, enabling higher quality fulfillment as it allows both pickers and packers to identify what products go in what order.
Single shipment picking means only one shipment basket is handled at a time, which reduces picking mistakes or mix ups.
On top of increasing reliability and decreasing human-error, this solution is very easy to implement and to onboard new pickers. When new pickers are needed to satisfy a sudden increase in order fulfillment, it takes less than a minute to train them for this picking method, and therefore can start picking efficiently and in a timely manner. Hence, saving time, money, and flexibility when your brand experiences peak volumes.
On the other hand, because of the simplicity of this method, shipments are picked one by one, hence increasing the walking distance for the picker. This takes more time and effort, and slows the fulfillment process of the order.
All in all, this solution is effective for every e-commerce brand thanks to its simplicity.
Group picking
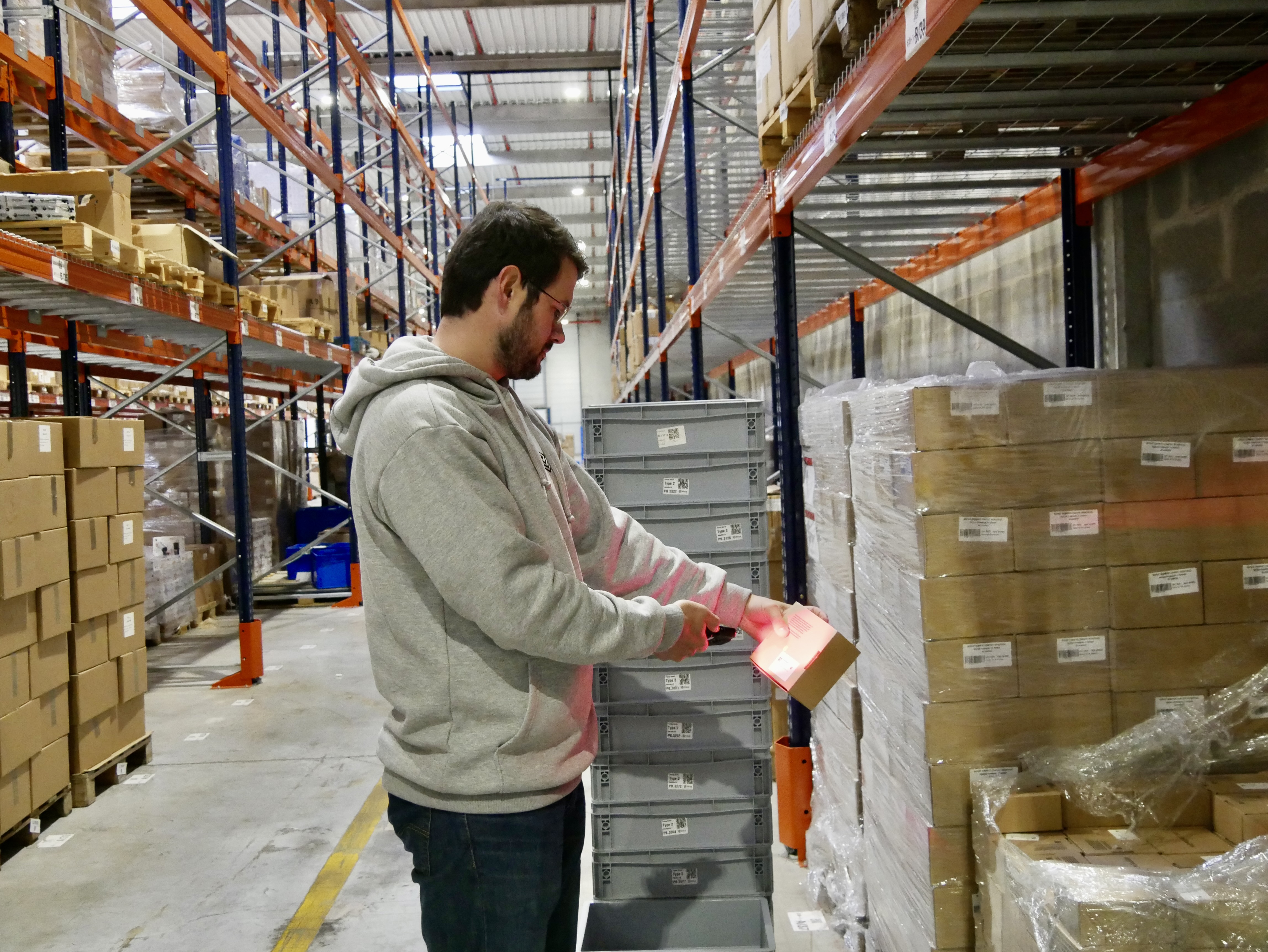
In group picking, the picker will be picking many single SKU shipments in a group. This is used when multiple orders have the same SKU and therefore the picker stays at this storage shelf, picking the single SKU for each order.
This method is extremely efficient as it reduces the walking distance and time that tend to slow down fulfillment in the single shipment picking process. In fact, group picking is 3 to 4 times as efficient as picking the same shipments in single shipment picking. The average picking time is reduced from 4 minutes to 40 seconds.
This picking method is highly efficient if you are a brand with many single SKU shipments.
Cart picking
This newest addition to the Hive picking portfolio enables the picker to pick multiple shipments with one or more SKUs from the same merchant in only one picking round.
In this solution, the picker brings along a large cart where all picking baskets are kept. When they start to pick, they must tell the system how many picking baskets are used in this round. Based on this input, the system will run an algorithm to create a group of most similar shipments that will lead to the most efficient picking round.
This solution helps maximize efficiency by dividing the walking distance by the number of shipments picked in a round. It is the most ergonomic solution and most efficient thanks to the grouping of similar SKUs and multi SKU shipments.
Cart picking is efficient for every brand, however, this solution will be most effective if you have many orders with similar SKUs, for example, if you have launched a marketing campaign on a specific bundle.
Bulk picking
Bulk picking refers to the picking of large quantities of SKUs, typically for large B2B orders. As such, the picker will complete all shipments in one order, rather than many individual shipments at a time like in the single shipment method.
If necessary, the system will break the order down into several picking tasks that allow optimized picking of large quantities.
Bulk picking essentially enables full pallet picking with forklifts, parallel execution of picking tasks for the same order by several pickers, and an efficient picking of large quantities. It is most effective for any brand that sends B2B orders.
Why picking at Hive means the best solution for your brand
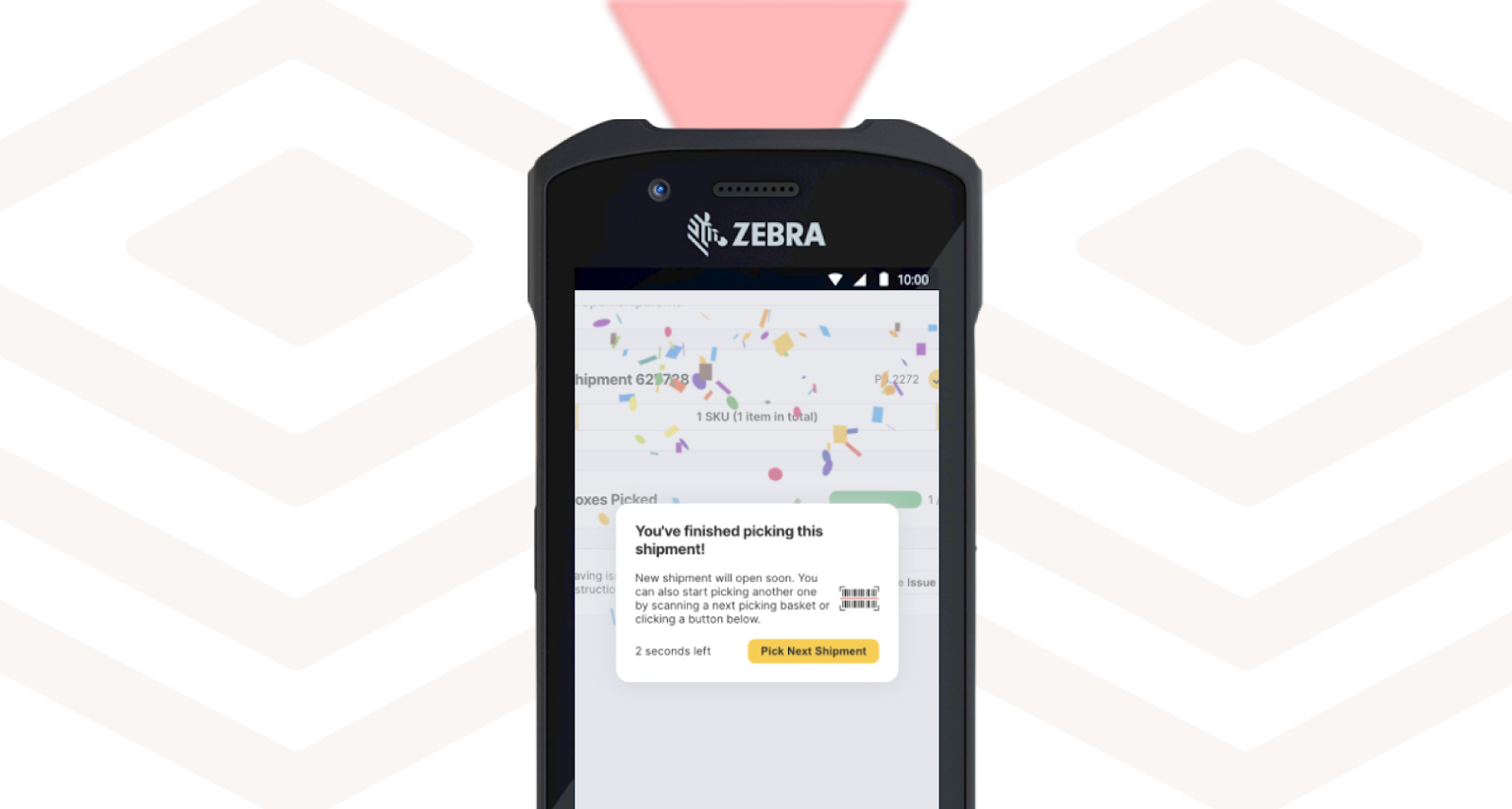
Picking at Hive is in constant evolution, with new solutions that are improved in order to optimize fulfillment for e-commerce brands. Our digitized system provides a 100% user-focused app that has been developed by our product, tech teams and specialized designers.
Multiple scan points for accuracy
In order to complete an order, the app is programmed with several scanning points which the picker has to scan individually before moving on to the next order.
This solution minimizes human error as it does not permit the picker to move on without scanning each correct barcode. In addition, this solution works with real time inventory updates that deduct inventory from the storage box in the moment that it is confirmed, and pickers can alert inventory discrepancies,triggering an automatic investigation task.
The number of scanning points have been optimized for a well-balanced tradeoff between efficiency and quality control which results in a user-friendly WMS interface that automatically prevents errors.
Gamified picking
In addition, the Hive WMS picking app has been gamified with sound feedback that emits different sounds when a picker completes an order, scans the right code, or the wrong one. This minimizes errors and allows the picker to scan without actually looking at the screen, allowing them to move more quickly.
Finally, the application is also configured to set off a confetti explosion on the screen every time an order is completely picked. Picking progress is also recorded and tracked to see how each picker performs, and to visualize the progress during the day. This solution helps motivate pickers to set new records constantly, improving efficiency and motivating them in their work thanks to positive feedback.
By gamifying and digitizing Hive’s picking methods, the software has been optimized in a way to reduce error, reduce the lead time, and increase productivity. This impacts the entire fulfillment process, improving performance for your brand, reducing your costs, and optimizing your end customers’ experience.